あなたはヒューマンエラーが無くならないことを悩んだことはありませんか?
モノづくりをしていると、不良が発生することがあります。
その不良の原因の一つにヒューマンエラーがあり、多くの企業でヒューマンエラー対策を考えています。
しかし、ヒューマンエラーの対策は「チェック表を管理」「作業者教育」で終わることが多く、再発防止にならないことがあります。
今回は私の経験を踏まえてヒューマンエラーについて発生する仕組みや要因、種類と対策など紹介します。
この記事を書いた人
- 当ブログ「アキシブログ/AKISHI blog」の管理人
- 産業機械メーカー(中小企業)の管理職を22年経験
- モノづくり現場の人材教育、生産性改善などのセミナーで講師を務めています
この記事を読んで欲しい人
- 製造業の管理者や作業者
- モノづくり現場にてヒューマンエラーで悩んで人
- ヒューマンエラーの解決方法を知りたい人
- 生産性向上のためミスをなくしたいと考えている人
ヒューマンエラーが発生する仕組み
人はミスをする要因を持っており、それらはすべてコントロールできるものでもないですが、それを知ることである程度、ミスの予防はできます。
作業の物理的状態や作業特性、作業者、管理者との人間関係、作業者の意識や健康状態、職場の管理状況など、様々な要因があり、この要因一つでもヒューマンエラーは発生します。
また、要因が複数になればより発生の確率は高くなります。
これらの要因を詳しく分析すると、対策は立てやすいでしょう。
ヒューマンエラー発生要因
内的要因
作業者自身の要因
性別、年齢、体質、体調、性格、感情、意欲、習慣、経験、熟練などが作業者の内的要因になります。
作業者自身の要因は種類が多く、わかりにくい要因もあります。
事例1:精密金属プレスを行っている会社で、部品検査で傷を見落とすミスが発生しました。
この現場は、作業後に品質管理チームが目視にて全数検査をします。
検査員は中堅社員で、いつもなら見落とすはずもない傷を見落とすミスをしてしまいました。
検査員は体調不良(風邪)だったことがわかり、薬を飲んでいたため集中力が続かなかったことが見落とす要因の一つと考えられます。
作業にもよりますが、人が集中できるのは20分程度が限界といわれており、体調不良がより集中力を欠く原因だったと言えるでしょう。
集中力はこのような体調不良だけでなく、年齢、体質、性格、感情なども影響するので注意が必要です。
作業者自身の内的要因は申告してもらえればわかるのですが、他者はわからないこともありますね。
それらを気づくためにも、管理者や周囲の作業者とのコミュニケーションが重要になってくるでしょう。
外的要因
作業環境や、使用する設備・治工具に問題はないか?
事例2:産業機械の電気配線ボックスを製作している会社の電気配線を行う現場で、配線ミスが発生しました。
現場にて原因を追究したときに夕日がミスの要因の一つだったことがありました。
その現場は、夕方になると夕日が作業場に入るので窓には遮光シート貼って対策をしていたのですが、たまたま換気のため、数センチ開いた窓から夕陽が入り、その夕日で配線の色がわかりにくく、白色と黄色の配線を間違えたことがありました。
現場責任者は、単に人による配線間違いとして処理してしまったのですが、よく作業者に聞いてみると、夕方は配線が見にくいときがあったということから夕陽がミス(ヒューマンエラー)を起こした要因の一つでと考えたことがあります。
このような作業場の明るさや、温度、騒音、臭いなどはヒューマンエラーを引き起こす外的要因となります。
また、設備や治工具についても、
重さ、重すぎる、力がいる、軽すぎる
距離、近すぎる、遠すぎる、高い、低い
時間、早すぎる、遅すぎる、慌ただしい
視聴覚、見にくい、眩しい、聞こえにくい、臭い
形態、持ちにくい、やりにくい
これらも外的要因になります。
その他にも、管理者による要因も外的要因になることがあります。
職場内のコミュニケーションや連絡方法、教育や訓練のしくみ、作業標準の有無や不備などを管理者が適切な状態にしていない場合、ヒューマンエラーが発生します。
事例3:製缶溶接の現場で、若手社員に溶接作業を行っていた時、溶接不良が発生しました。
作業者は溶接の免許を取得しており、毎日TIG溶接作業をしていましたが不良を作ってしましました。
原因は教育と訓練不足です。
管理者はTIG溶接作業が出来るだろうと思って作業をさせていましたが、実際は毎日1.2ミリの鉄板をTIG溶接しており、今回の不良品は6ミリの鉄板でした。
不具合内容は溶け込み不足で、管理者が6ミリの溶接の教育は行っていましたが、訓練させていなかったため、作業者は溶け込み不良を出してしまったのです。
教育は「知らないことを伝えること」で、訓練は「伝えたことが出来るようになること」なのです。
管理者は知識伝え溶接見本は見せたくらいで終わってしましました。
テストピースを準備して溶接状態を何度か確認したかが重要で、確実に出来るようになったことを確認しなければ訓練は終わりません。
同じTIG溶接でも板厚が変われば、出来ないことは十分考えられるので、しっかり確認するべきだったと思います。
また、管理者と作業者が十分にコミュニケーションを取れていたら、教育の段階で気づけたかもしれません。
このようにヒューマンエラーは内的要因ばかりでなく、外的要因が引き起こすヒューマンエラーあるので注意が必要です。
ミスの種類と対策
- ポカミス:ぽかんとして忘れたりすること
- (対策)注意・規律・標準作業
- パナシミス:適切な指示も標準作業もなく作業者に任せっぱなし
- (対策)標準作業・作業指導
- アマミス:知らない作業や生半可な作業
- (対策)標準作業・作業指導法
- アレミス:予期した動きをしないで「アレ」と思わせる
- (対策)TPM活動・標準作業
- ウッカリミス:うっかりしていたり、忘れていたり
- (対策)事前確認・定期確認・呼称確認
- カッテミス:この程度ならかまわないと勝手に決め込む
- (対策)基礎教育・躾・習慣化
- チラミス:見落とし、ちらっと見ただけ
- (対策)打合せ・注意
- ガッテンミス:気が早かったり、勘違い
- (対策)事前確認・作業標準
- ニブミス:判断の遅れにより、反応や動作の遅れ
- (対策)熟練・作業標準
- ワザミス:わざと犯す
- (対策)基礎教育・躾
このようにミスの種類は多く、それぞれに有効な対策も変わってきます。
ミスの状態を現地・現物・現実の三現主義で確認し、要因分析を行い適切な対策を取るとよいでしょう。
ヒューマンエラーの解析フロー図
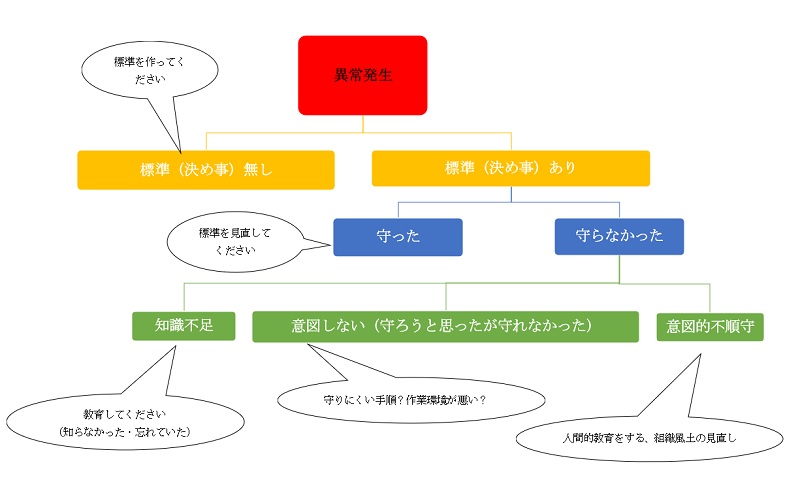
このフロー図を使えば、ある程度の要因はつかめると思います。
新任管理者などへの教育材料として使ってください。
まとめ
不良や不具合、ミスには何らかの原因があります。
今回ヒューマンエラーについて紹介しましたが、すべての原因を人とするのではなくヒューマンエラーが発生した仕組みに注目し、改善対策を行うべきでしょう。
そのためには原因の分析が重要になってきます。
正しい分析を行い、仕組み改善を行い、あなたの企業のヒューマンエラーがなくなること目指しましょう。
最後まで読んでいただきありがとうございます。