製造業では誰もが知っている5Sですが、大切だと知っていてもなかなか継続できない企業があるのではないでしょう?
私も製造現場がもっと5Sをしっかりやって欲しいと思った時期もありました。
この記事では私の経験を踏まえ、5Sを行ってもらうための管理側の考え方と進め方を紹介します。
この記事を書いた人
- 当ブログ「アキシブログ/AKISHI blog」の管理人
- 産業機械メーカー(中小企業)の管理職を22年経験
- モノづくり現場の人材教育、生産性改善などのセミナーで講師を務めています
- 企業で5S指導も行っています
この記事を読んで欲しい人
- 製造業の管理者や作業者
- モノづくり現場にて5Sの必要性を知りたい人
- 5Sを実践している人
- 企業の5Sを推進している人
- 生産性向上のため5Sを構築したい人
5Sとは?
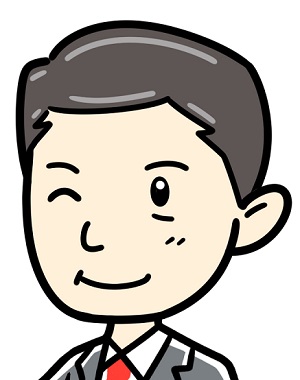
5Sとは、整理(SEIRI)・整頓(SEITON)・清掃(SEISOU)・清潔(SEIKETU)・躾(SHITUKE)の5つで頭文字のSが5つあるので5Sと呼んでいます
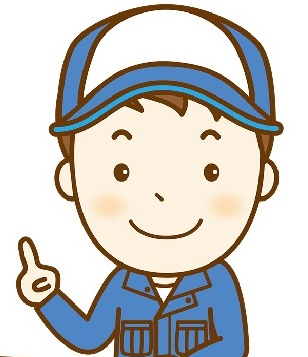
製造業の多くの方は知っていますよね。
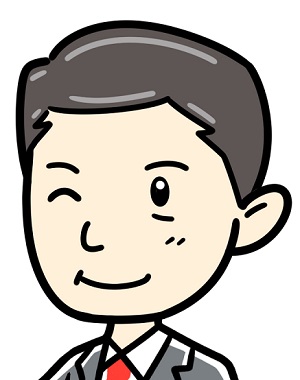
この記事は5Sを定着させる考え方や仕組みを紹介しますよ。
5Sの目的・目標・納期を明確にしていますか?
人は目的がわかり納得すると、より能動的に動きます。
そして目標があると、どこに向かって行けばわかるので迷うことはなくなりますね。
また、期日(納期)を決まれば、それを守ろうとします。
このことから、5Sの目的、目標、納期を決めて周知することで、4Sが継続し、それが躾となり5Sを達成できるようになります。
この目的、目標、納期は、出来るだけ具体的に示すとより分かりやすく周知も容易になり、5Sは継続できるでしょう。
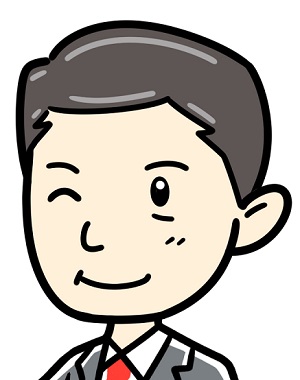
能動的に動いてもらうには、目的をしっかり伝えることが大切ですね
5Sの目的 あなたの会社では何を伝えていますか?
5Sの目的は「生産性の向上」だけで終わらせる企業が多くあります。
片付けと生産性が向上することに繋がらない社員は多いのではないでしょうか?
特に入社間もない社員は、よくわからないまま5Sしてくださいと言われ、片付けることが目的になっていると継続しませんね。
どのような状態だと生産性が良くて、どのような状態だと生産性が悪いのかを明確に説明し体験してもらうことが重要です。
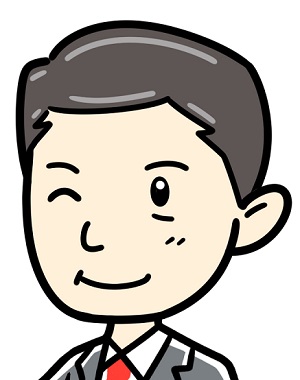
良い状態を体感してもらって、生産のやり易さを実感してもらってくださいね!
また、5Sがお客様へ与える影響もあります。
5Sにより不良品が少なくなれば、品質が高い会社と認識されます。
同じ商品を2社で作っておりライバル会社の5Sがしっかりできていてそのことがお客さんに伝われば、そちらで購入する人は多いでしょう。
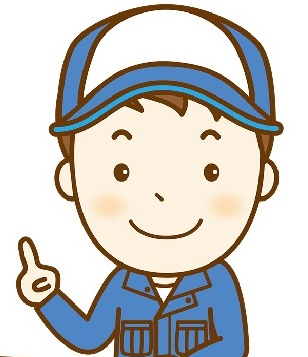
きちんとした会社でものは買いたいですよね!
これらのことより、5Sは営業支援にも十分なります。
また、最近では学生に対しインターシップ研修を行う企業も増えてきました。
学生が企業を決めるとき、きれいなだった会社を選ぶ学生の方が多いはずです。
5Sの目的は「生産性の向上」という言葉で終わらせるのではなく、5S生産性を体験し、整った会社は営業活動やリクルート活動にも影響があることを知ってもらい、これらすべてを目的として伝えることが大切です。
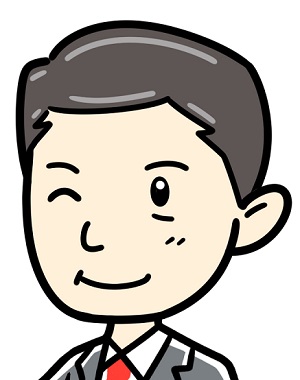
5Sによる様々な効果を伝えることが、管理者の仕事ですよ!
5Sの目標 どのレベルを目指していますか?
「整理・整頓をしっかりしましょう」 「きれいな作業場にしましょう」
こんな標語は製造現場によくあります。
そして管理者もよく言いますね。
この言葉をどれだけ言っても、現場は変わらないでしょう。
これは価値観の違いの影響です。
人は年齢・性別・国籍・性格・育ってきた環境など、様々なことから同じ人間は存在しません。
たまたま価値観が同じような人はいると思います。
それはたまたまで、企業には千差万別十人十色の人間が集まるわけですから、「しっかり」や「きれいな」のような言葉は曖昧になり、人によっては十分出来ていると思う人がいるでしょう。
話し合いでも定義を確認してから話し合うことと同じで、5Sの完成した状態を管理者と作業者と合わせる必要があります。
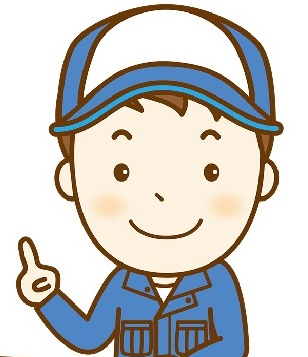
価値観を合わせることが大切なんですね!
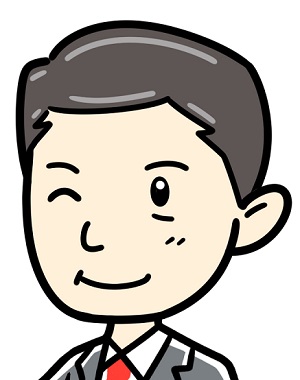
多様化する時代で5Sを通して価値観を合わせることが5Sの目的の一つにもなりますよ
これは相当レベルの高い会社では、必要ないことかもしれませんが多くの企業では必要でしょう。
この5Sの完成した状態も企業によって大きく変わります。
全く5Sができていない町工場が急に大手自動車メーカーのような状態にするのは、ハードルが高いかもしれません。
超えれないハードルは、結局できないで終わるか、やる気がなくなるかになります。
少しだけ、背伸びをしたくらいの5Sを目指して、目標を達成できることを重視してください。
達成感はかなり重要でその後の5S活動にも影響してきます。
出来るだけ達成することを目指してください。
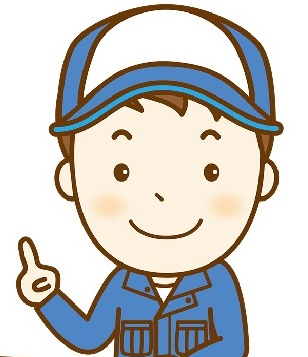
そもそもできない目標はモチベーション上がりませんよね
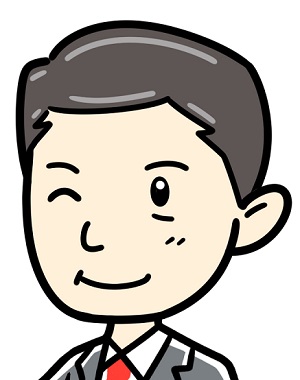
適正な目標を作ることも管理者の仕事ですね
目標の作り方ですが、数値化出来ればいいのですが、初期の5S活動では数値化は難しいです。
数値での目標設定が難しいと判断した場合、「あるべき姿」を共有してください。
そのあるべき姿は、近隣の工場などで良い見本があれば、管理者と作業者で見学させてもらい目指すべき内容の共有をすることがいいでしょう。
他社などの工場見学ができなければ、一部の作業場を管理者と作業者で協力して5S活動を行い、その作業場を基準とする方法もあります。
どちらの方法も、どのような状態が「あるべき姿」なのかを目で見て共有することが大切です。
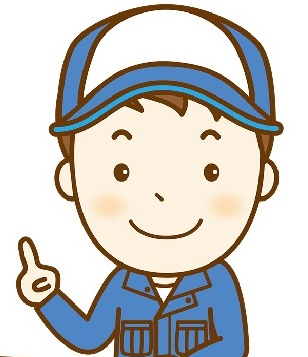
あるべき姿を見える形にして共有しよう!
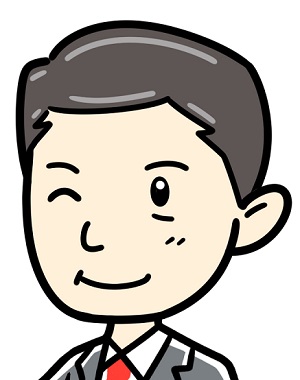
あるべき姿は、皆さんで描いてくださいね。
5Sの期限(納期)はいつまでですか?
年末の大掃除にいらないものがたくさん出てきて、「よし!来年は5Sを徹底的に行う!」と宣言する経営者や幹部社員がいます。
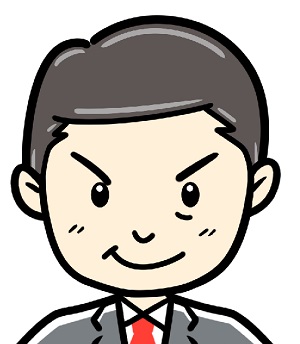
来年は徹底的に5Sを行うぞ!
宣言した経営者や幹部社員が年明けから毎日休みなく5S状況を確認し続ければ、5Sが継続されるかもしれません。
しかし、多くの企業では正月休みと年始の忙しさで、すぐに忘れ去られることが多いのではないでしょうか?
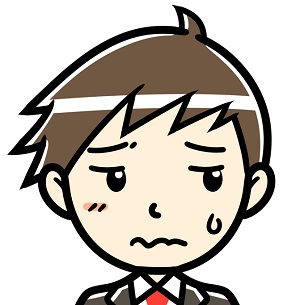
社長!忙しくて、5S活動は出来ません!!!
専門専属の管理者を作り、その人は5Sしか仕事が無ければ続くかもしれませんが、人材にそんな余裕がある会社も少ないです。
そうすると、仕組みを使ってどうやって継続するかになります。
私が最適だと考える仕組みはPDCAサイクルです。
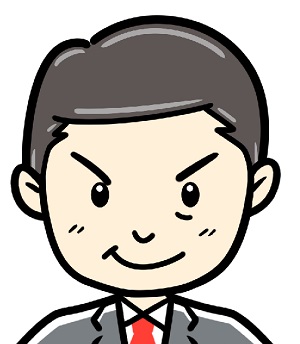
よし! PDCAを使おう。計画をたてるよう!
- 経営者や幹部社員は毎月の確認
- 管理職は毎週の確認
- 管理職以下の方(作業者など)は毎日の確認を行います。
これは役職や立場によってPDCAを回すサイクルを変える方法です。
現場の最先端の作業者は毎日作業を行っているわけですから、小さな範囲で毎日5Sを少しづつ行い、その積み重ねが週間になり、月間、年間それぞれの周期でPDCAサイクル使って管理する手法になります。
役職にあわせて範囲や周期を管理するやり方になりますね。
役職が高い方が、細かく隅々まで5Sを管理することはできないことが多く、それが風化の原因にもなります。
細かいことは部下に任せますが、任せっぱなしにならないように細かなPDCAが大きなPDCAにつながる仕組みで管理することをお勧めします。
具体的な5S活動の進め方
一般的には整理・整頓・清掃・清潔・躾の順で進めます。
ここでは具体的な私のやり方を紹介します。
整理
必要なものと不要なものに分けます。
最終的に不要なものは捨てることになりますが、これは私が苦手で、なかなかものが捨てれません。そんな方は多いのではないでしょうか?
リーダーは何をやるか?ではなく何をやらないか?の判断することが重要と言われています。
このことから整理を行うとき何を捨てるかを決断することがリーダーの訓練だと思って一生懸命捨てますが、それでも私は苦手ですね。
そこで私は整頓から始めます。
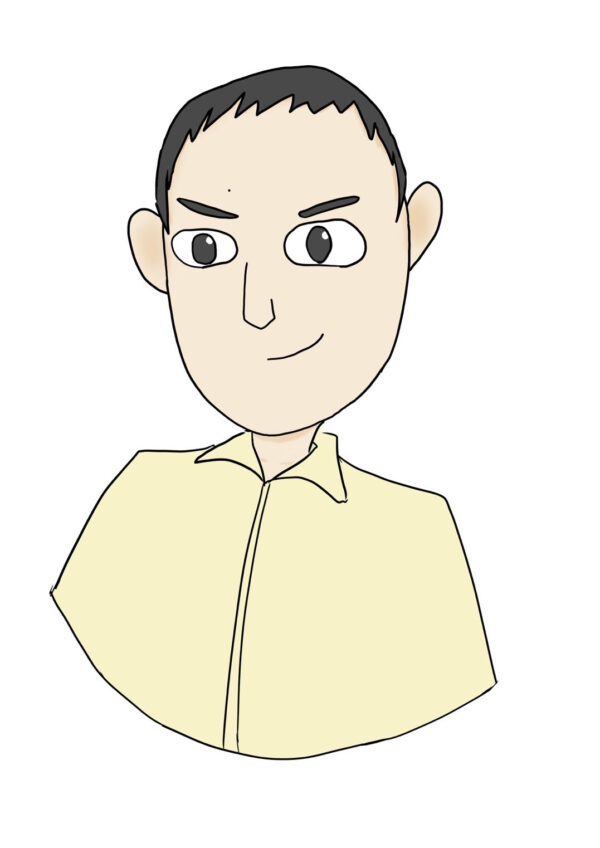
私は、物が捨てれない人でした。だから整頓から始めましたよ!
整頓
物を置く場所を決めます。
そしてそこに置きますが、整理が出来ていないと置けません。
それは不要なのではないかと考え、捨てるか、少し遠くに置きます。
遠くに置く場合は期限を決めて使わなければ捨てることにしています。
だから、整頓がかなり重要になってきて、どこの範囲まで5Sを行いたいかで整頓の方法が変わってきます。
清掃
整理・整頓がしっかりできてくると清掃はかなりやり易いし、やりがいも出てきます。
ここで重要なのが、パートナーです。
パートナーと言っても異性でなくても大丈夫で、部下や後輩でもいいので誰かを巻き込むことが出来ると良いでしょう。
清掃は忘れがちになることと、相手がしっかりやっているから自分もやらなければみたいな気持ちが出てくることが多いですよね。
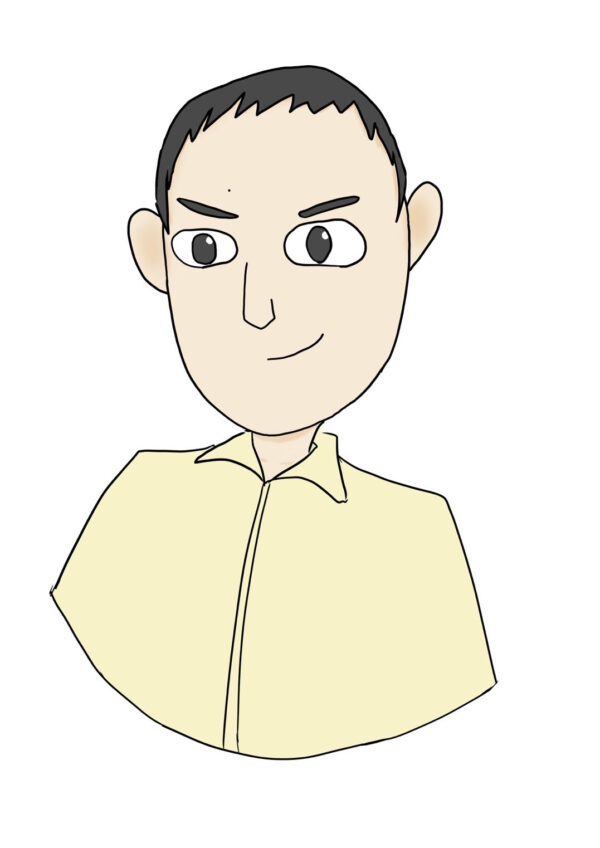
私は部下に刺激を受けてモーレツに清掃をしたことがありますよ!
また、パートナーがいてもお互いに忙しく忘れてしまうことがあります。
そんなときは、自動的に音楽やアラームを流し、その音楽やアラームが鳴ったら清掃タイムになる仕組みがあると継続もしやすいでしょう。
清潔
清潔の状態の認識は人によって大きく変わります。
製造現場の清潔は定義を作ることが難しいかもしれませんね。
私は多くの金属加工製造業を見させていただきましたが、これは本当に様々でした。
ただ、言えることはとてつもなく清潔な金属加工業社でも、そこまでたどり着くのにかなりの時間をかけているということです。
整理・整頓・清掃のレベルを少しずつ高め、びっくりするようなピカピカの工場に仕上げたのでしょう。
一般的にはそこそこのレベルで清潔は止まってしまいます。
それは、感覚がマヒしてくることがあるからです。
もし、それ以上を目指すなら、全く関係ない人に指摘してもらうことをお勧めします。
業界が全く違う人や、学生、もしくは従業員の家族なんかもいいかもしれません。 違う目線で、どこが汚いかを教えてもらい、さらにレベルの高い清潔を目指すことも良いでしょう。
躾
躾は決められたことをしっかり守ることです。
躾が出来ていれば、整理・整頓・清掃・清潔は決め事なので必ずうまく行きます。
なのでこれらがうまく行かない理由は躾なのです。
やはりこの躾が一番難しく、管理者が悩むことが多いのではないでしょうか?
具体的に目的・目標・納期を明確にしてPDCAを回し仕組みで進めると言いましたが、 最終的には経営者や管理者の躾が部下の躾になり、経営者・管理者の姿が部下の姿になります。
部下の躾を言う前に自分の躾を見直すことが重要かもしれません。
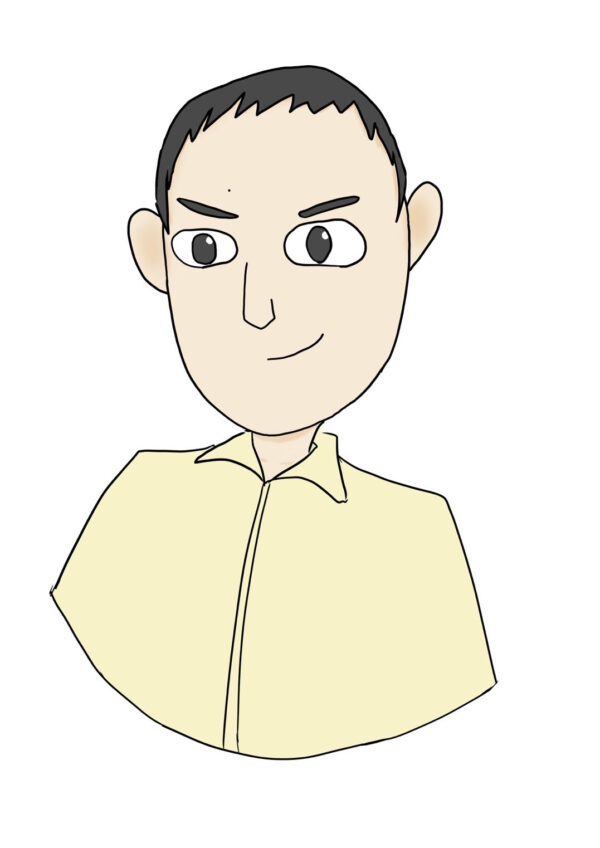
部下は上司をよく見ていますよ!まずは自分が変わらなくてはダメですね
まとめ
5Sで会社の状況はある程度把握できます。
ぐちゃぐちゃで会社の業績が良い企業は少ないでしょう。
5Sが出来ないのは、ある程度の仕組みと経営者・管理者の覚悟だと思います。
この記事の仕組みを参考にしてもらい、経営者・管理者がやる気を出せばきっと5Sはうまく行くでしょう。
日本が生んだ5Sという仕組みをしっかり運用し、あなたの会社が業績を伸ばしていただけると幸いです。
最後まで読んでいただきありがとうございます。
製造業のヒューマンエラーの記事もあります。是非読んでください。
管理者の考えと行動しだいで製造現場は5Sできるようになりますよ!